Intro
Discover 5 innovative ways foam forms enhance construction, packaging, and crafting, offering versatility, insulation, and protection, while exploring related techniques like foam cutting and molding.
The versatility of foam is undeniable, and its applications span across various industries, including construction, packaging, and even healthcare. Foam forms are an essential component in many manufacturing processes, offering a range of benefits that make them an ideal choice for numerous applications. In this article, we will delve into the world of foam forms, exploring their importance, benefits, and the various ways they are utilized.
Foam forms are created through a process that involves mixing raw materials, such as polyurethane or polyethylene, with air or gas, resulting in a lightweight, yet durable, material. The unique properties of foam make it an attractive option for companies seeking to reduce costs, improve efficiency, and enhance product performance. From cushioning and insulation to filtration and soundproofing, the uses of foam forms are diverse and continue to expand as technology advances.
The significance of foam forms cannot be overstated, as they play a crucial role in shaping the modern world. Whether it's the comfortable seating in our cars, the insulation in our homes, or the packaging that protects our goods during shipping, foam forms are an integral part of our daily lives. As we move forward, it's essential to understand the various ways foam forms are used and the benefits they provide, allowing us to harness their full potential and explore new applications.
Introduction to Foam Forms
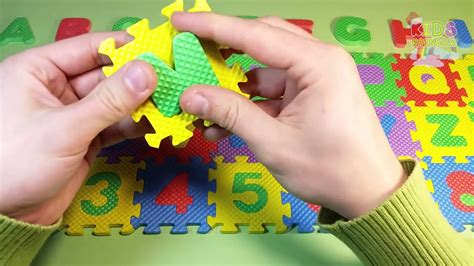
Types of Foam Forms
The classification of foam forms is based on their density, which is measured in pounds per cubic foot (PCF). The density of foam affects its strength, durability, and performance, making it essential to choose the right type of foam for a particular application. Some common types of foam include: * Low-density foam: Used for packaging, cushioning, and insulation * Medium-density foam: Used for seating, bedding, and soundproofing * High-density foam: Used for industrial applications, such as filtration and sealingApplications of Foam Forms
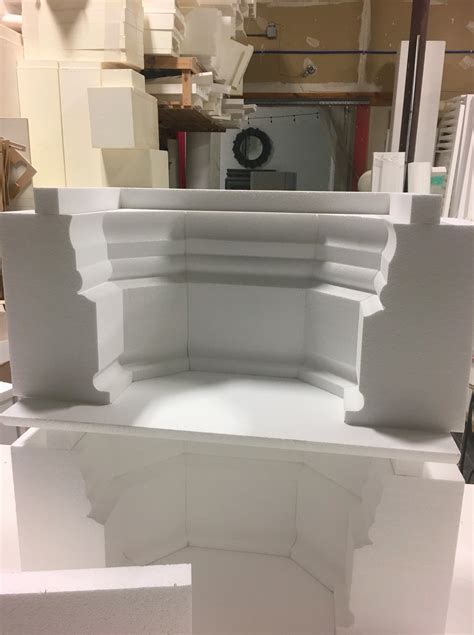
Benefits of Foam Forms
The benefits of foam forms are numerous, making them an attractive option for companies seeking to improve efficiency, reduce costs, and enhance product performance. Some of the most significant benefits of foam forms include: * Lightweight: Foam is significantly lighter than traditional materials, making it easier to transport and handle * Durability: Foam is resistant to wear and tear, providing long-term performance and reducing maintenance costs * Versatility: Foam can be molded into various shapes and forms, making it suitable for a wide range of applications * Cost-effective: Foam is often less expensive than traditional materials, providing a cost-effective solution for companiesManufacturing Process of Foam Forms
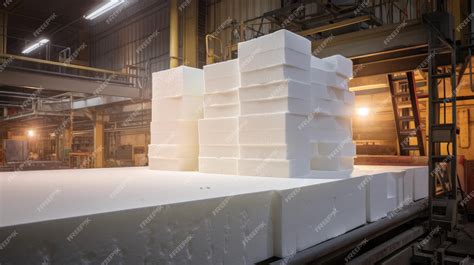
Quality Control and Testing
Quality control and testing are essential in ensuring that foam forms meet the required standards and specifications. Some of the most common tests used to evaluate foam include: * Density testing: Measures the density of the foam to ensure it meets the required specifications * Compression testing: Measures the compressive strength of the foam to ensure it can withstand the required loads * Tensile testing: Measures the tensile strength of the foam to ensure it can withstand the required stressesFuture of Foam Forms

Challenges and Opportunities
Despite the many benefits and applications of foam forms, there are also challenges and opportunities that need to be addressed. Some of the most significant challenges include: * Environmental concerns: The production and disposal of foam materials can have environmental impacts, such as pollution and waste * Competition from alternative materials: The development of alternative materials, such as recycled plastics, is posing a challenge to the foam industry * Regulatory compliance: Foam manufacturers must comply with regulations and standards, such as those related to safety and environmental protectionWhat are foam forms used for?
+Foam forms are used for a variety of applications, including cushioning, insulation, filtration, soundproofing, and seating and bedding.
What are the benefits of foam forms?
+The benefits of foam forms include their lightweight, durability, versatility, and cost-effectiveness, making them an attractive option for companies seeking to improve efficiency and reduce costs.
How are foam forms manufactured?
+Foam forms are manufactured by mixing raw materials with air or gas, resulting in a lightweight, yet durable, material. The process typically involves mixing, foaming, shaping, and curing.
As we conclude our exploration of foam forms, it's clear that these versatile materials play a vital role in shaping the modern world. From their unique properties and benefits to their wide range of applications, foam forms are an essential component in various industries. We invite you to share your thoughts and experiences with foam forms, and to explore the many ways they can be used to improve efficiency, reduce costs, and enhance product performance. Whether you're a manufacturer, a designer, or simply a curious individual, we encourage you to join the conversation and discover the many wonders of foam forms.