Intro
Discover average labor time explained, including labor hours, repair times, and standard labor rates, to help estimate job costs and increase efficiency in workforce management and automotive repair industries.
The concept of average labor time is a crucial aspect of various industries, including manufacturing, construction, and services. It refers to the amount of time it takes for a worker or a team to complete a specific task or project. Understanding average labor time is essential for businesses to optimize their operations, improve productivity, and reduce costs. In this article, we will delve into the world of average labor time, exploring its importance, calculation methods, and applications.
Average labor time is a critical component of labor costing, which is the process of determining the cost of labor for a particular project or task. By calculating the average labor time, businesses can estimate the total labor cost and make informed decisions about pricing, resource allocation, and project scheduling. Moreover, average labor time helps companies to identify areas of inefficiency and implement process improvements to increase productivity and reduce waste. As a result, understanding average labor time is vital for businesses to remain competitive in today's fast-paced market.
The calculation of average labor time involves several factors, including the type of task, the skill level of the workers, and the equipment used. For instance, a construction company may need to calculate the average labor time for building a house, taking into account the number of workers, their skill levels, and the type of materials used. Similarly, a manufacturing company may need to calculate the average labor time for producing a specific product, considering factors such as machine efficiency, worker training, and quality control. By analyzing these factors, businesses can determine the average labor time and make adjustments to optimize their operations.
Average Labor Time Calculation Methods
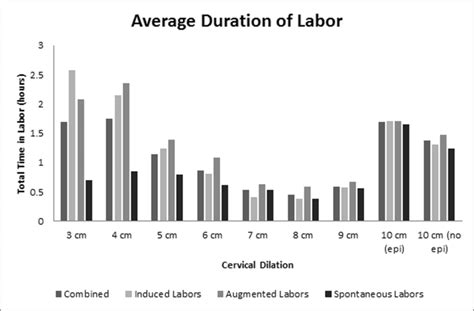
There are several methods for calculating average labor time, including the stopwatch method, the work sampling method, and the standard data method. The stopwatch method involves measuring the time it takes for a worker to complete a specific task using a stopwatch. This method is simple and straightforward but may not be accurate for complex tasks or tasks that involve multiple workers. The work sampling method involves observing workers at random intervals to determine the amount of time spent on a specific task. This method provides a more accurate estimate of average labor time but may be time-consuming and expensive. The standard data method involves using pre-determined standard times for specific tasks, which can be obtained from industry benchmarks or historical data. This method is quick and easy to use but may not be accurate for unique or complex tasks.
Stopwatch Method
The stopwatch method is a simple and straightforward way to calculate average labor time. It involves measuring the time it takes for a worker to complete a specific task using a stopwatch. This method is useful for simple tasks that involve a single worker, such as assembling a product or performing a maintenance task. However, it may not be accurate for complex tasks that involve multiple workers or tasks that require a high level of skill or expertise.Work Sampling Method
The work sampling method involves observing workers at random intervals to determine the amount of time spent on a specific task. This method provides a more accurate estimate of average labor time than the stopwatch method, as it takes into account the variability of task times and the impact of external factors such as equipment breakdowns or material shortages. However, it may be time-consuming and expensive to implement, especially for large-scale projects or tasks that involve multiple workers.Standard Data Method
The standard data method involves using pre-determined standard times for specific tasks, which can be obtained from industry benchmarks or historical data. This method is quick and easy to use, as it eliminates the need for direct observation or measurement. However, it may not be accurate for unique or complex tasks that do not have established standard times.Average Labor Time Applications
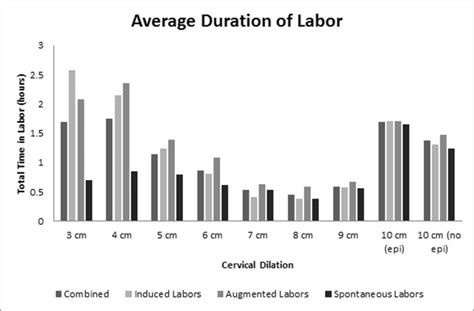
Average labor time has numerous applications in various industries, including manufacturing, construction, and services. In manufacturing, average labor time is used to estimate the labor cost of producing a specific product, taking into account factors such as machine efficiency, worker training, and quality control. In construction, average labor time is used to estimate the labor cost of building a specific project, considering factors such as the number of workers, their skill levels, and the type of materials used. In services, average labor time is used to estimate the labor cost of providing a specific service, such as healthcare or consulting, taking into account factors such as the skill level of the workers, the type of equipment used, and the level of customer service required.
Manufacturing Industry
In the manufacturing industry, average labor time is used to estimate the labor cost of producing a specific product. This involves calculating the average labor time for each task involved in the production process, such as assembly, inspection, and packaging. By analyzing these times, manufacturers can identify areas of inefficiency and implement process improvements to increase productivity and reduce waste.Construction Industry
In the construction industry, average labor time is used to estimate the labor cost of building a specific project. This involves calculating the average labor time for each task involved in the construction process, such as excavation, foundation work, and finishing. By analyzing these times, contractors can identify areas of inefficiency and implement process improvements to increase productivity and reduce waste.Service Industry
In the service industry, average labor time is used to estimate the labor cost of providing a specific service. This involves calculating the average labor time for each task involved in the service delivery process, such as consultation, diagnosis, and treatment. By analyzing these times, service providers can identify areas of inefficiency and implement process improvements to increase productivity and reduce waste.Average Labor Time Benefits
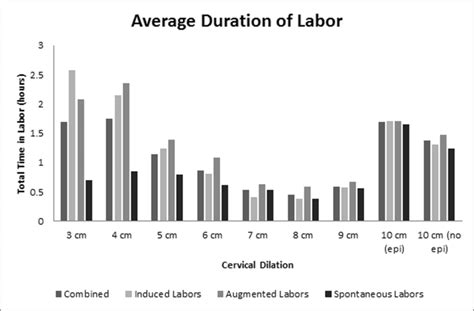
The benefits of average labor time are numerous and significant. By calculating average labor time, businesses can estimate the total labor cost and make informed decisions about pricing, resource allocation, and project scheduling. Average labor time also helps companies to identify areas of inefficiency and implement process improvements to increase productivity and reduce waste. Additionally, average labor time enables businesses to compare their performance with industry benchmarks and competitors, allowing them to identify areas for improvement and develop strategies to gain a competitive advantage.
Improved Productivity
One of the primary benefits of average labor time is improved productivity. By analyzing average labor times, businesses can identify areas of inefficiency and implement process improvements to increase productivity and reduce waste. This can be achieved by streamlining workflows, reducing unnecessary tasks, and providing workers with the necessary training and equipment to perform their jobs efficiently.Reduced Labor Costs
Another benefit of average labor time is reduced labor costs. By estimating the total labor cost, businesses can make informed decisions about pricing, resource allocation, and project scheduling. This can help to reduce labor costs by avoiding overstaffing, minimizing overtime, and optimizing worker utilization.Enhanced Competitiveness
Average labor time also enables businesses to compare their performance with industry benchmarks and competitors, allowing them to identify areas for improvement and develop strategies to gain a competitive advantage. By analyzing average labor times, businesses can identify areas where they can improve their performance and develop strategies to increase their competitiveness in the market.Average Labor Time Challenges
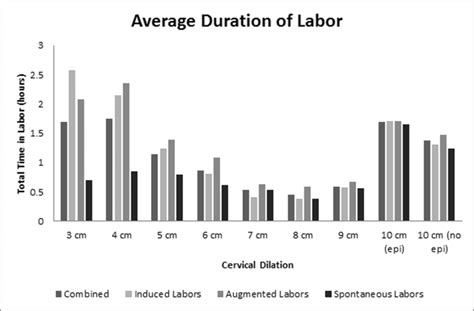
Despite the benefits of average labor time, there are several challenges associated with its calculation and application. One of the primary challenges is the accuracy of the data used to calculate average labor time. If the data is inaccurate or incomplete, the calculated average labor time may not reflect the actual time it takes to complete a task, leading to incorrect estimates of labor costs and productivity.
Data Accuracy
The accuracy of the data used to calculate average labor time is crucial. If the data is inaccurate or incomplete, the calculated average labor time may not reflect the actual time it takes to complete a task, leading to incorrect estimates of labor costs and productivity. Therefore, it is essential to ensure that the data used to calculate average labor time is accurate, complete, and up-to-date.Task Variability
Another challenge associated with average labor time is task variability. Tasks can vary significantly in terms of complexity, duration, and skill requirements, making it challenging to calculate an accurate average labor time. To address this challenge, businesses can use techniques such as work sampling or standard data to estimate average labor times for tasks with high variability.Worker Variability
Worker variability is another challenge associated with average labor time. Workers can vary significantly in terms of skill level, experience, and productivity, making it challenging to calculate an accurate average labor time. To address this challenge, businesses can use techniques such as worker training and performance evaluation to ensure that workers have the necessary skills and expertise to perform their jobs efficiently.What is average labor time?
+Average labor time refers to the amount of time it takes for a worker or a team to complete a specific task or project.
How is average labor time calculated?
+Average labor time can be calculated using various methods, including the stopwatch method, the work sampling method, and the standard data method.
What are the benefits of average labor time?
+The benefits of average labor time include improved productivity, reduced labor costs, and enhanced competitiveness.
What are the challenges associated with average labor time?
+The challenges associated with average labor time include data accuracy, task variability, and worker variability.
How can businesses overcome the challenges associated with average labor time?
+Businesses can overcome the challenges associated with average labor time by using techniques such as work sampling, standard data, and worker training to ensure accurate and reliable data.
In conclusion, average labor time is a critical component of labor costing and productivity analysis. By calculating average labor time, businesses can estimate the total labor cost, identify areas of inefficiency, and implement process improvements to increase productivity and reduce waste. While there are challenges associated with average labor time, such as data accuracy, task variability, and worker variability, businesses can overcome these challenges by using techniques such as work sampling, standard data, and worker training. We invite you to share your thoughts and experiences with average labor time in the comments section below. Additionally, if you found this article informative and helpful, please share it with your colleagues and friends who may benefit from learning about average labor time.